Brazed Construction
The next level up in chassis design would be a brazed construction. A brazed chassis could be either dip or vacuum braze based on the requirements. In general, a dip brazed chassis is easier and less complex than a vacuum brace and dip brazed is best suited for open channel geometry. The open channel geometry allows the molten salt to easily flow out of the chassis without becoming trapped. An example of an open channel geometry would be folded fin brazed to a cold wall provide extended surface area for a force convection cold chassis. In a dip braze chassis typically the four walls and any extended surface area are put through the dip process to provide both good structural rigidity as well as improve thermal transfer.
A vacuum brazed chassis is more suited for closed channel geometry where the path through the chassis appears completely sealed and where the presents of trapped salt may not be permitted by application. An example would be a chassis designed for liquid cooling where the liquid path may exist in multiple pieces or where there parallel passages for the liquid. In these it would be difficult to flush the part and ensure all salt is removed. When working with either brazed chassis method the design of the joints is a critical aspect both to achieve maximum strength and the complex shape that may be required. Wakefield Thermal prefers that you consult with us prior to specifying the joint type or location or provide us with a monolithic model so that we can review and determine how best to place the joints.
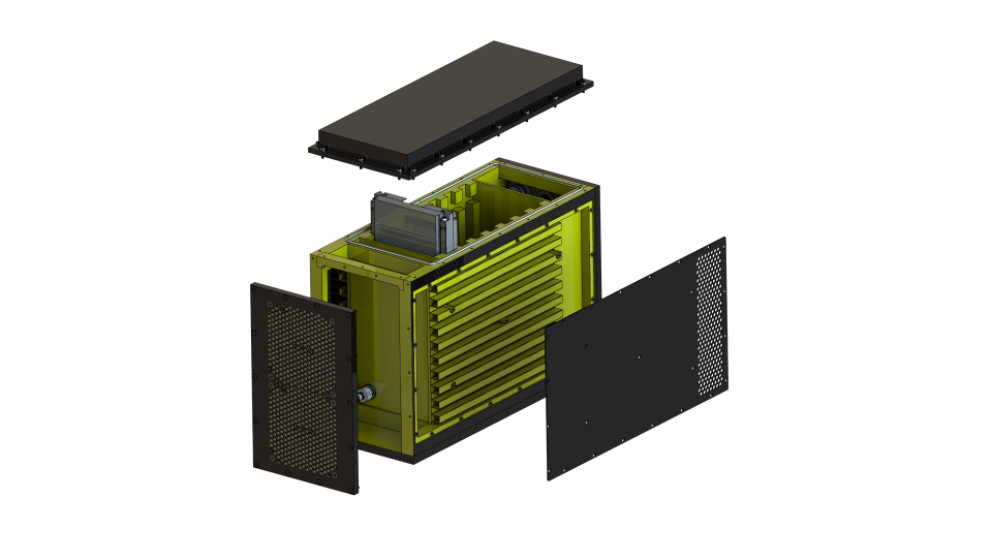